MillPart Extends Production Time 7 Hours with Global AGV
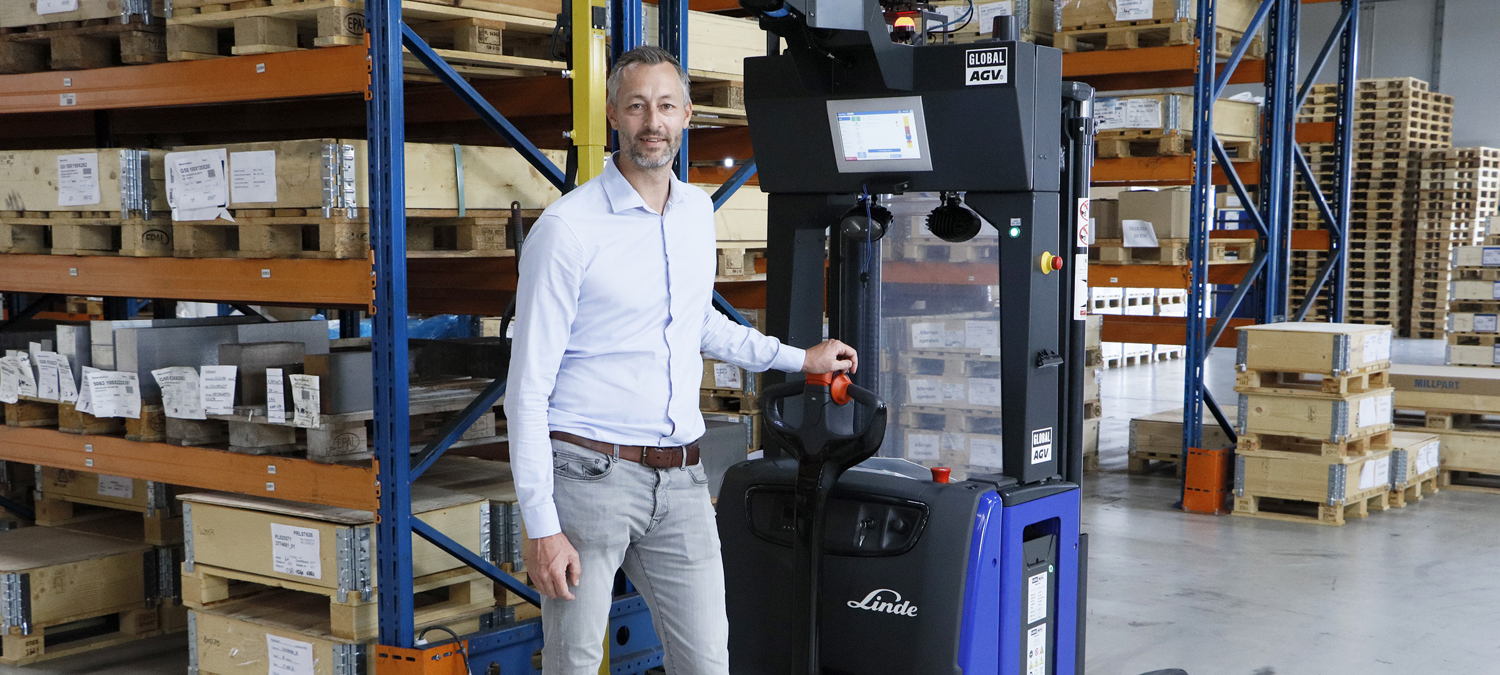
Extended production
time by 6-7 hours
MillPart provides hydraulic components to global companies and boasts one of Denmark's most advanced machine facilities. Prioritising quality without compromise, MillPart places a strong emphasis on leveraging automation in both production processes and enhancing the working environment. Their recent investment in a new robot cell presented the perfect opportunity to incorporate Global AGV to automate numerous heavy pallet transfers to and from these robot cells.
Stable production
without fluctuations
Improved
work environment
Fewer
bottlenecks
Added an extra
shift per day
Challende
At MillPart, it used to be a manual process to 'feed' their robot cells with raw materials. This led to bottlenecks and line stoppages because their robot cells ran out of raw materials—and they didn't restart until an employee noticed it.
Solution
With the AGV, MillPart can now 'feed up' and ensure that there is raw material for the robot cells for well over 24 hours, thereby maintaining a smooth flow in production.
Gain
Specifically, this means they can keep the production line running for an additional 6-7 hours beyond their regular working hours – naturally resulting in increased production capacity and the full usage of their machines.

Fewer bottlenecks and one extra shift per day
Production line bottlenecks and stoppages are both expensive and unsustainable. At MillPart, they had the recurring challenge of many irregularities in their robot cells because they ran out of raw materials.
The AGV has resolved this challenge.
The Global AGV’s implementation means that today they have more stable production and can run one extra shift per day without additional staff.
The need for stable and steady production was of great importance for the AGV investment.
"We wanted to minimise fluctuations due to high activity and staff shortages. With Global AGV, we can maintain a smooth production flow. Before, an operator had to move the pallets manually. Therefore, we often had stoppages on the line because it had run out of raw material – and it did not run again until an employee discovered the stoppage. With the AGV, we can “feed up” and make sure there is raw material for well over 24 hours,"
Tom Nørsten, Production Manager at MillPart
Specifically, this means that they can keep the production line running for 6-7 hours longer than their regular working hours – and making full use of the machines has naturally increased production capacity.
Seamless installation in just three days
For MillPart, it was essential to have a reliable solution successfully implemented in other companies. According to Tom Nørsten, Production Manager at MillPart, the installation went completely painlessly.
“It's all just worked.”
That’s it. But we still got Tom to add a few more words:
"I’m pleasantly surprised by how quickly and smoothly the AGV was implemented. Once everything was ready from our side, it took just three days. It then ran non-stop for 24 hours – and has run without problems ever since. It’s also great that it’s a tried and tested solution, so we didn’t serve as guinea pigs."
Tom Nørsten, Production Manager at MillPart
Protects employees from heavy lifting
Another – just as important – reason to implement an AGV is the working environment. The AGV now handles what used to be an arduous task for the work teams. Today, Global AGV handles moving the heavy metal blocks around the production hall – previously a manual task for the operators, using a pallet stacker.
"When the technology exists, it makes no sense for our employees to wear themselves out with moving the heavy blocks. It’s also highly motivating for both us and our employees to invest in new technology that can make the work run more smoothly," says Tom Nørsten.
Interested in learning more about Global AGV?
Send us a message, and we'll look at the possibilities.
Or call us at +45 96 69 47 10.
Contact us
We are ready to answer all your
questions and discuss all the possibilities
of production optimisation in your company.