Welltec Leverages Employee Resources Better with Global AGV
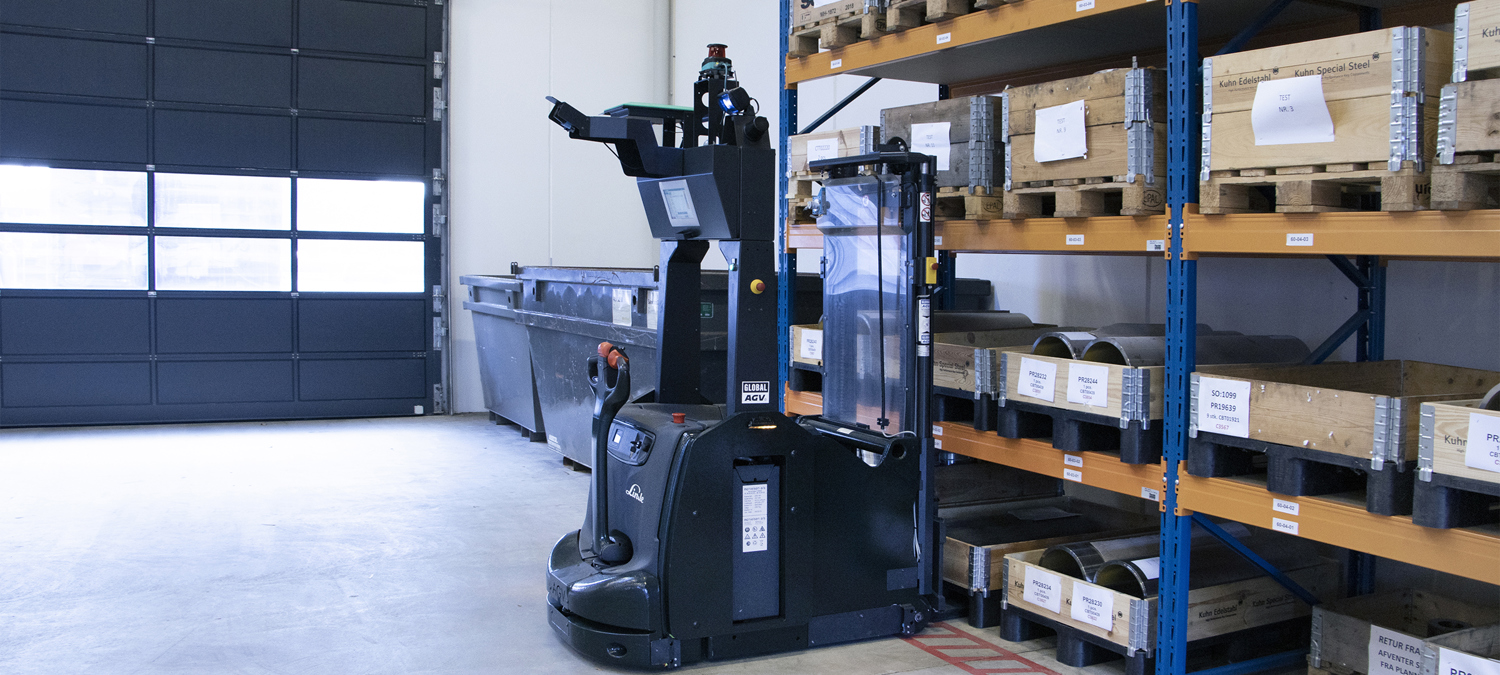
Welltec leverages employee
resources better with Global AGV
With Global AGV, Welltec can enhance production by efficiently transporting raw materials from saw to manufacturing, optimising employee resource utilisation, achieving smoother production, and ensuring a future-proof production environment.
Transport of raw materials to the production area
Increased productivity
Better flow in production
Future-proof setup
Challenge
To ensure increased efficiency and create a better working environment, there has been a significant focus on automating workflows at Welltec's factory in Esbjerg.
Solution
As part of that process, Welltec deployed a Global AGV to transport raw materials to and from the production area.
Profit
This has enabled the utilisation of knowledge and employee skills in a much more effective manner, benefiting both the employees and the company.
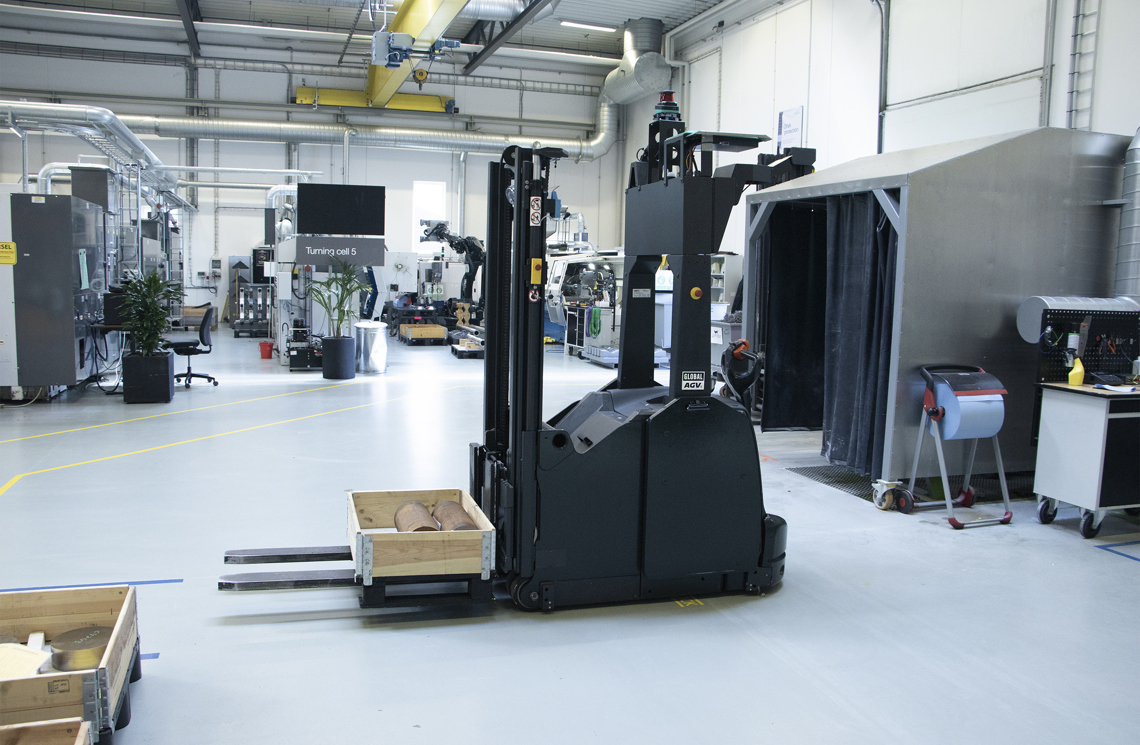
Efficiency improvement and better utilization of employee competencies created a need for automation
Located by the roaring waves of the North Sea in Esbjerg, Welltec develops and produces hi-tech solutions for the energy sector worldwide. Welltec's groundbreaking products are designed to optimise well performance in any environment, and their solutions have helped customers increase operational efficiency and reduce their CO2 footprint in a safe and sustainable manner for over 25 years.
Welltec's factory in Esbjerg runs like a well-oiled machine, with large robot systems supplying the CNC machines with components and tools. Since the establishment of the factory, there has been a strong focus on automating workflows, both to ensure increased efficiency and to create a better working environment.
As part of this process, Welltec introduced a Global AGV to transport raw materials to and from the production area. This has ensured a smooth flow without bottlenecks, freed up employee time, and minimised interruptions in production.
"Previously, when we had to transport raw materials from the saw to our CNC department, the saw operator had to drive back and forth. Today, we let the AGV handle it. That means we don't have to take someone out of production just to fetch a pallet,"
Haris Medosevic, CNC Coordinator at Welltec in Esbjerg
Particularly the shortage of employees with forklift certification has posed challenges.
"There is a significant shortage of employees with forklift certifications in the CNC department. That has made us heavily dependent on those individuals whenever a pallet needed to be transported to a new location, and it has sometimes limited us. With the planning of our workflows, we can now assign the AGV to retrieve the different pallets we need, without requiring the saw operator to go and fetch them"
Challenges with wheel spin were solved through a software upgrade
When new technology is implemented in a production environment, it often brings local challenges. The same was true at Welltec. The floors where the AGV was to operate were very slippery, making it difficult for the AGV to gain traction, resulting in wheel spins on the smooth floor. With navigation primarily relying on wheels (80%) rather than sensors (20%), it caused navigation issues.
Technicians addressed the problem by updating the underlying software, shifting the control more towards the sensors. According to Haris Medosevic, there have been no issues with the collaboration with Global AGV.
"We recently upgraded our AGV, which brought several improvements. The challenge was that the AGV's navigation relied 80% on wheels and 20% on sensors. However, due to our very smooth floor, it caused wheel spin, causing the AGV to think it was one meter ahead or behind its actual position. The team at Global AGV has been a great help, always ready to assist. After some tests, they provided a solution that works 110%. So our collaboration with Global AGV has been excellent."
Haris Medosevic, CNC Coordinator at Welltec in Esbjerg
Looking a few years into the future, it is clear that the AGV will be incorporated into future expansions of the production lines as well.
"The plan is to expand eventually, and in that process, Global AGV will also be involved in transporting materials and filling the spaces in production."
Haris Medosevic states.
Interested in learning more about Global AGV?
Send us a message, and we'll look at the possibilities.
Or call us at +45 96 69 47 10.
Contact us
We are ready to answer all your
questions and discuss all the possibilities
of production optimisation in your company.