What is an AGV and Why Should You Buy One?
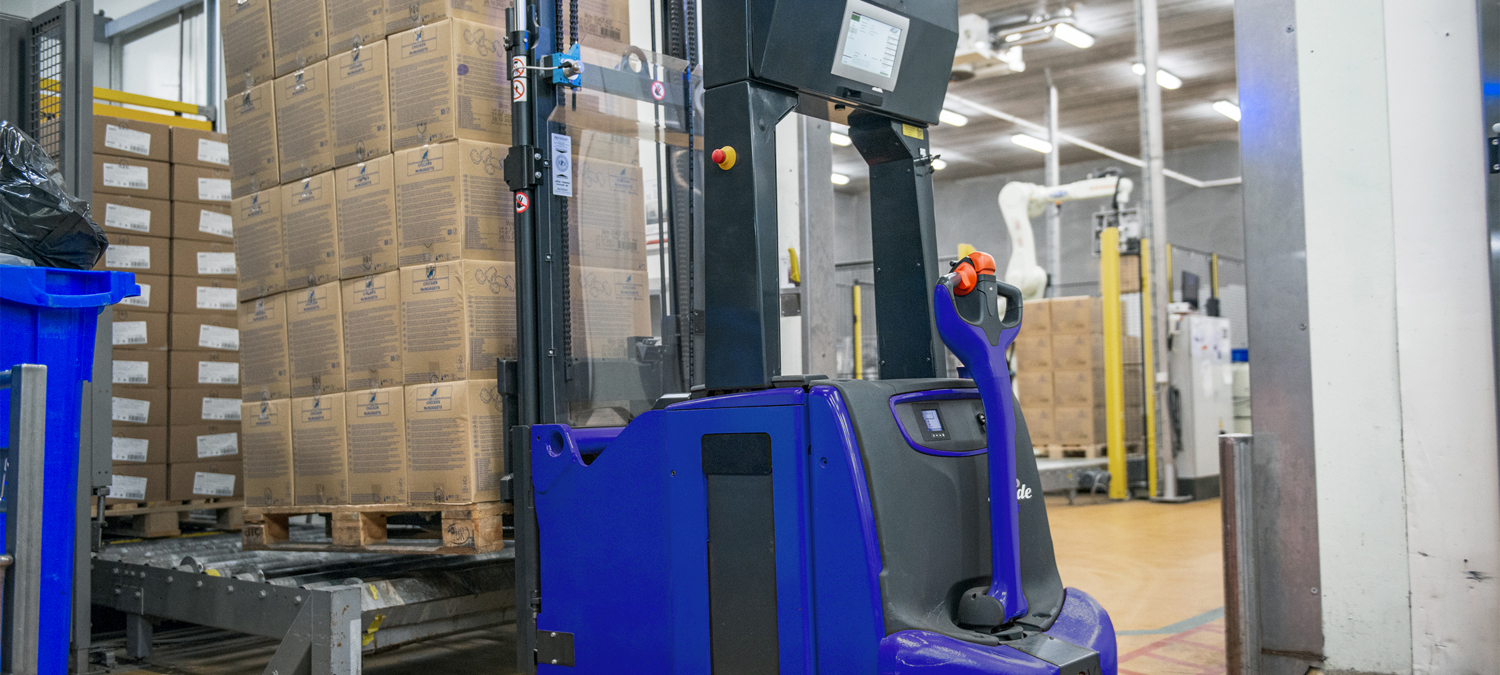
Discover How AGVs Increase Efficiency, Reduce Costs, and Free Up Resources
Automated Guided Vehicles (AGVs) have revolutionised how we approach logistics and material handling in various industries. These innovative automated pallet movers have brought significant improvements to production facilities, warehouses, and distribution centres.
This blog will unfold:
The world of AGVs
Their benefits
How they work
Their applications in different situations
The basics: What are Automated Guided Vehicles?
AGV stands for Automated Guided Vehicles – or All-time Great Workmate, which we like to call it.
Because that's what it is.
It's a tireless workhorse that works around the clock, never needs a break (except for short periods of charging time) and never complains about overtime.
Who doesn't want a co-worker like that?
More technically, AGVs are unmanned forklift trucks used in manufacturing plants and warehouses to automate tasks traditionally performed by human workers using forklifts.
They are designed to move autonomously, either following a predetermined path or using advanced navigation systems to find the most efficient route.
AGVs can carry a wide range of payloads, from small parts to large pallets, and can be customised to suit specific industry requirements.
But how do AGVs work?
There are different types of AGVs – but all of them are equipped with advanced features and guidance systems that help them manoeuvre around their surroundings efficiently and effectively.
By combining these features and capabilities, AGVs can effectively undertake pallet transports, serving as an invaluable asset in an automated facility.
These features include:
Guidance Systems
The guidance system can, e.g., be sensors, cameras or wires embedded in the floor which emit a magnetic field which the AGVs sensors can detect and follow.
Route Programming
AGVs can be configured to follow specific paths, stopping at prescribed locations, providing a level of predictability and consistency in their operations.
Communication Abilities
AGVs can communicate with other AGVs or automation systems within the facility. This increases their collaborative capabilities, enhancing overall productivity.

The benefits of AGVs
The million-dollar question remains:
Why should I invest in an AGV?
Well, there are numerous benefits to implementing forklift AGVs in your production facilities and warehouses, including:
-
Improved safety: Did you know 87 people in the US are killed yearly due to truck accidents? Or that 95 are seriously injured daily? AGVs are a safe alternative to manually driven trucks because they have sensors and safety features that help prevent accidents and collisions with workers or other equipment.
-
Reduced cost of errors: Do you know how much you spend yearly on repairs due to truck collisions? Or have you ever had to do something manually (like foil wrapping) while waiting for a piece of equipment to be repaired? When a truck collides, it not only causes damage to what it hits – there is also a risk of affecting production. By automating truck driving, AGVs minimise the chances of human error, such as misplaced items or damaged goods, leading to cost savings.
-
Increased efficiency: AGVs can operate continuously, 24/7, without getting tired or becoming inattentive, and they don’t need breaks or shift changes. That is why you can achieve higher efficiency with an AGV. This allows for increased productivity and faster order fulfilment. All-time Great Workmate, right?
-
Scalability: Scaling your production up and down becomes much easier with an AGV. AGVs can be easily integrated into your existing operations as your business grows, allowing for a smooth expansion of your material handling capabilities. For instance, you can upgrade from 1 to 2 shifts (or 3) without hiring more people. You can also scale up periodically during high seasons or if you land a huge order at no additional cost.
-
Flexibility: AGVs can be reprogrammed or reconfigured to adapt to changing production needs, making them versatile solutions for various applications. Psst… And with Global AGV, you can even reconfigure them yourself. They are so easy to manage that you don't need our help.
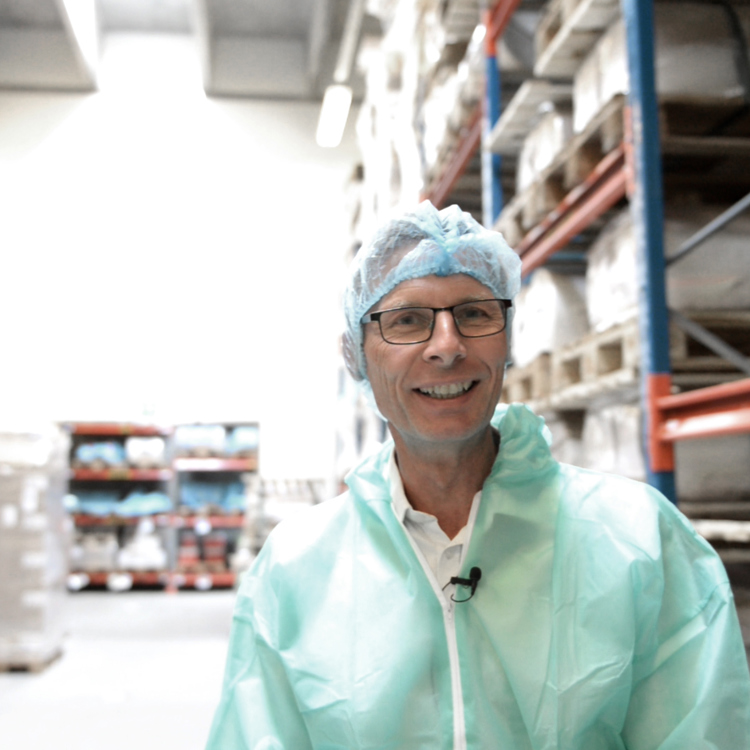
End-of-line transport
Palletisers, wrappers and pallet dispensers are all great equipment on their own, but when they team up, it's a productivity powerhouse.
And AGVs play an essential role in this automation dream team.
Imagine this:
A simple palletising setup where AGVs pick up pallets from the dispenser, feed them to the robotic palletiser, drive the full pallet to the wrapper, and zip it off to the warehouse – all without breaking a sweat.
No human involvement.
Just robots working in perfect harmony.
The repetitive transports at the end-of-line offer a significant return on investment (ROI) and prompt payback – especially for operations running multiple shifts.
See how A. Espersen reduces bottlenecks and wasted time at their fish plant logistics centre with Global AGV.
Pick-up or drop-off at fixed stations or in rows
Do you place pallets in rows?
For instance, at a waiting area, where the pallets are distributed to different places?
AGVs can help with that. The AGV can pick up pallets from around your production facility and drop them off in rows in a storage area. The sensors detect where the next pallet is placed in the row and will accurately place the pallets in defined lanes on the floor.
See how Welltec leverage employee resources better with Global AGV
Long-distance pallet transport
Having a lot of long-distance pallet transports?
No worry.
Forklift AGVs excel in the long-distance transportation of pallets within a production facility. They efficiently bridge the gap between different areas within a large factory, shuttling goods back and forth.
Their programmed routes help optimise traffic flow in facilities reducing bottlenecks and downtime.
See how A&O Johansen saves 60-80% on their internal logistics by letting 3 Global AGVs take over the daily handling of 800 pallets.
AGV Business Case
Investing in AGVs is a downright game-changer—in our humble opinion, of course. And we know you're curious to learn more about the financial benefits.
We get it.
You want to know your investment pays off.
And it will.
Investing in AGVs can lead to substantial cost savings and operational improvements for businesses. By automating material handling processes, companies can reduce labour costs, minimise errors, and increase efficiency.
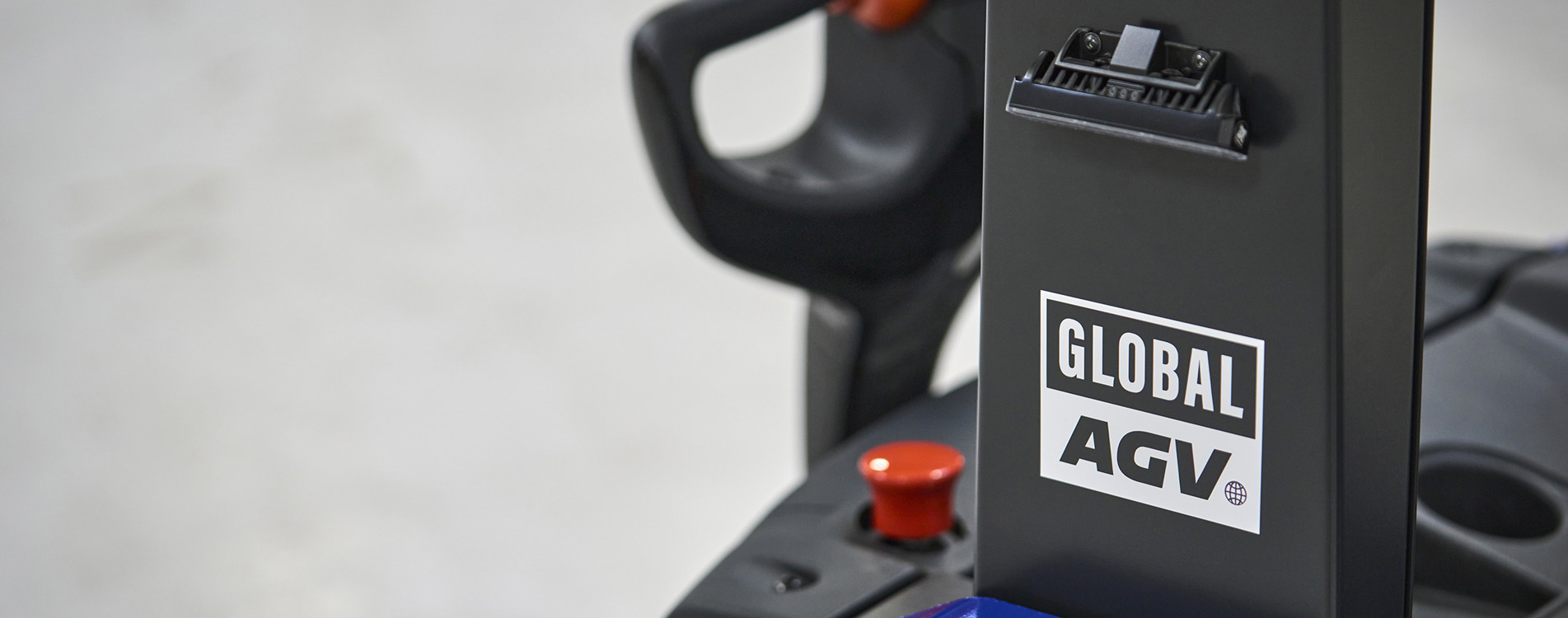
Interested in learning more about Global AGV?
Send us a message, and we'll look at the possibilities.
Or call us at +45 96 69 47 10.
Contact us
We are ready to answer all your
questions and discuss all the possibilities
of production optimisation in your company.